一、材料要求:
吊车梁规格为:H5600×1200×40×60 、H5500×1200×40×60、H5500×900×25×50,材质为Q345C,钢材应有良好的可焊性和合格的冲击韧性,钢材的强屈比不应小于1.2,应有明显的屈服台阶,钢材的伸长率应大于20%。钢材的化学成分应符合GB/T1591-94中相应钢材质量等级的规定,其中主要化学成分必须保证符合要求。所用埋弧焊的焊丝牌号为H08MnA,焊丝直径为φ4.0和φ5.0;焊剂牌号为SJ101,并且应在250℃温度下烘干2小时。气体保护焊采用的是80%为氩气20%为二氧化碳的富氩保护气体;药芯焊丝牌号为YJ-507,焊丝直径为φ1.2。手工电弧焊的焊条采用E5015,焊条直径为φ3.2和φ4.0,并且应在350℃温度下烘干1.5小时。
二、对接要求:
钢板对接焊缝采用X形对称坡口(见下图),先在一侧用气保焊打底,再反面清根用气保焊打底后,用埋弧自动焊填充及盖面,再翻身用埋弧自动焊填充、盖面,气保焊打底主要是控制变形,如果埋弧自动焊有把握则可以用埋弧自动焊以提高功效。埋弧自动焊打底电流控制为450A,填充电流750~800A,以保证有较大的熔深。采用分段退焊或跳焊法焊接,长度控制在1.5~2m。焊前预热120℃~150℃,焊接层间温度控制在150℃~200℃,后热温度控制在250℃,后热时间为2小时。整个焊接过程应连续,一条焊缝间隔时间不超过2小时。否则重新预热。
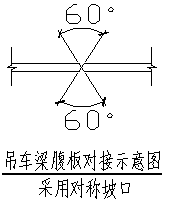
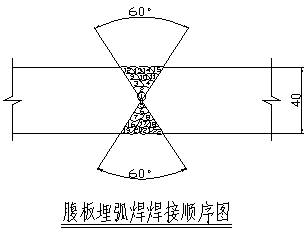
三、焊接制作总体要求:
吊车梁上下翼缘及腹板对接时要控制在吊车梁跨中1/3以外受力较小的部位,吊车梁上下翼板和腹板采用对接正焊缝拼接,拼接采用加引弧板施焊,引弧板其厚度和坡口与主材相同,焊缝等级二级,三者的对接焊缝不应设置在同一截面上,应相互错开200以上,与加劲肋宜错开200以上,所有吊车梁中间加劲肋与上翼缘连接处刨平顶紧后焊接。
吊车梁上翼缘与腹板的T形焊缝采用全熔透二级焊缝,吊车梁下翼缘与腹板的T形焊缝在两端距支座L/8(且不小于1m)的范围内采用全熔透二级焊缝,严禁在下翼缘上打火及焊接施工夹具,平板支座端加劲肋的上端与翼缘采用坡口熔透二级焊缝,下端与翼缘应刨平,并与下翼缘顶紧焊接,梁下支座处的窄垫板应与下翼缘板夹紧后焊接;突缘支座端加劲肋的下端应刨平;横向加劲肋下端点的焊缝应采用连续回焊后再灭弧,回焊长度不小于3倍直角焊缝焊脚尺寸。
吊车梁上翼缘板对接焊缝的上表面、下翼缘板对接焊缝的上下表面及所有引弧板割去处,均应机械加工,一般可用砂轮修磨使这与主体金属平整,吊车梁的下翼缘板边缘,当用手工气割或用剪切机切割时,应沿全长刨边,当用自动或半自动气割时不平整处应修理平整。
吊车梁的焊接需注意,焊接时必需采用翻身焊接,一根吊车梁打底焊时必须有两个焊工从中间向两边对称焊,先焊坡口深的一侧,再焊坡口浅的一侧,最后盖面坡口深的一侧,以适当的电流控制焊接变形和控制减少焊接内应力。
吊车梁按折线起拱,截面高度5600mm和5500mm按L/3000起拱。
吊车梁制孔:
1、由于吊车梁断面相当大,焊接成型后再制吊车梁上翼缘与制动桁架的高强螺栓连接孔不容易,在没有经验的情况下,可以采用制作首件,计算四条纵长焊缝的纵向收缩变形量,在翼缘板上的每组孔距中考虑焊接收缩余量,以保证高强度螺栓的穿孔率,先对翼缘板制孔再组焊成H型钢。长度方向的收缩值(供参考):板厚25mm,长度收缩值1.7mm、板厚40mm,长度收缩值2.2mm、板厚50mm,长度收缩值2.4mm、板厚60mm,长度收缩值2.9mm。
2、钳工钻孔时必须以中心线为基准。螺栓孔必须要在数控钻床上加工,以保证孔位置、尺寸的精度。考虑到构件的制作难度吊车梁制动螺栓孔可比相应螺栓大4mm,以利于安装。
3、孔的允许偏差超过设计或规范规定时,不得采用钢块填塞,应采用与母材材质相匹配的焊条补焊后重新制孔。
4、高强螺栓孔孔距的允许偏差应符合下表的规定(普通螺栓孔可放大一倍):
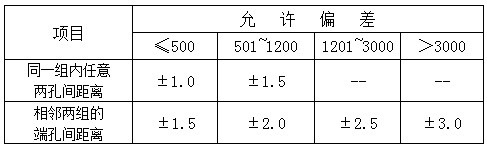
四、现场组装要求:
现场吊车梁翼板与腹板T形对接与角接组合采用卧式组立、焊接, 腹板采用不对称坡口,只需翻身两次就能完成H型钢焊接。组立、焊接胎架如下图,
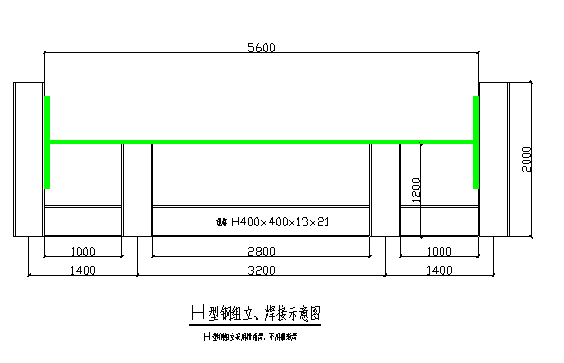
1、首先对现场的场地进行平整,然后搭设组装平台,平台间距3m 左右,立柱及横梁均用H400×400×13×21的热轧H型钢,如下图:
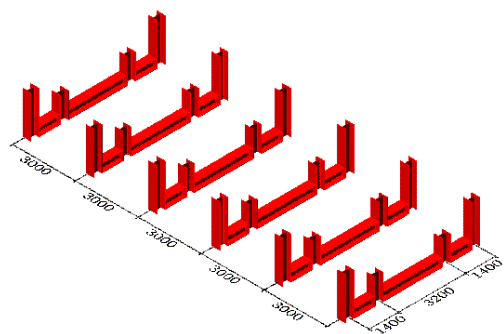
2、画好基准线,将已经拼接好的吊车梁腹板平放在胎架上,两侧放吊车梁翼板,进行卧式组立、焊接。如下图:
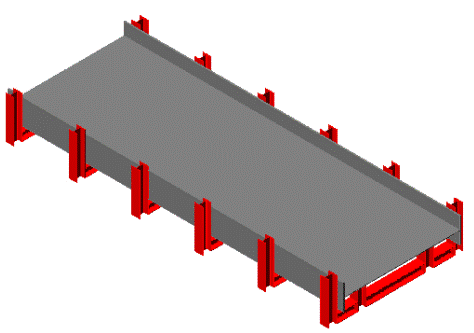
3、吊车梁组焊好后,进行吊车梁加筋的组对,如下图:
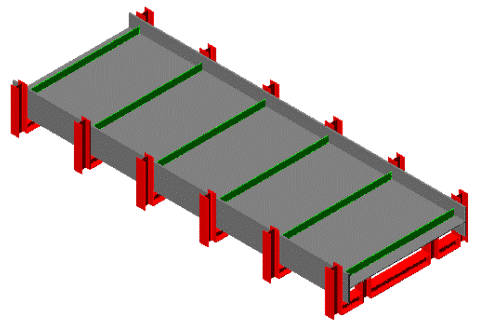
4、吊车梁分三段各自组拼完成后,最后采用立式总拼装,总拼时马凳高度300~500mm,吊车梁两侧采用型钢支撑对称加固,间距5~6m。腹板采用立焊,方向由中间向两端,打底及背面清根打底后,采用两名焊工同时对称分段焊接。最后焊接翼缘板。
……接下篇……