1 构件概况
特殊埋入箱形柱位于塔楼外框的角上,双向倾斜6度,由于2个面连接支撑,所以此柱子的断面为菱形,而水平剖面为矩形,设有纵向隔板和2层底板。三箱柱位于塔楼外框上,双向倾斜6度,断面为3箱矩形,而水平剖面为菱形,在外侧1箱设有巨大的蝶形连接板。
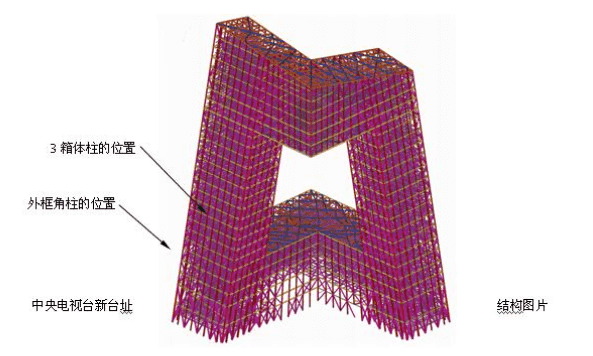
2 结构介绍
2.1外框角柱
外框角柱位于塔楼1的角部,构件在空间为双向6度内倾斜,构件的本体由地上段和埋入段组成,主体由板厚100mm的 Q390D—Z35厚板构成,底板厚为135mm的Q390D—Z35。角柱垂直于柱轴线的的截面为菱形,水平截面为矩形,两墙面侧有与斜撑相连的箱形牛腿,其中箱形牛腿的一块翼板为柱本体翼板的延伸。结构焊接型式为全焊透一级焊缝,角柱的净截面宽为1米╳1米,长度为10米,单根净重60吨。
角柱的结构图
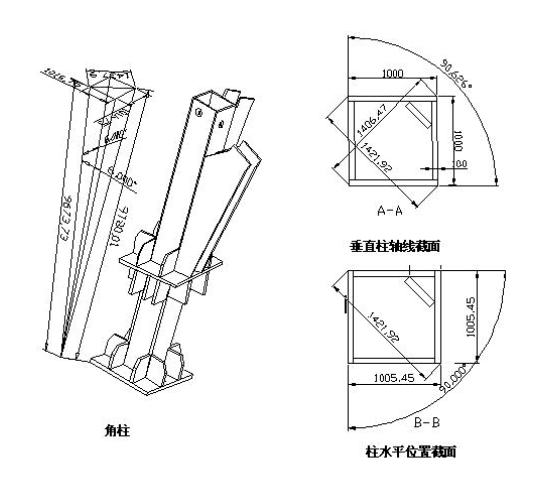
2.2三箱柱
外框3箱柱位于塔楼的外立面,构件在空间为双向6度内倾斜,与外框梁连接的牛腿为水平设置,柱子本体由板厚100mm的 Q420D—Z35厚板构成,多箱柱由3个箱体组成,外侧箱体的翼板通过蝶形板与箱形结构的斜撑相连,结构焊接型式为全焊透一级焊缝,3箱柱的净截面为1.4米╳1米,长度为14.88米,单根净重123吨。
三箱柱的结构图
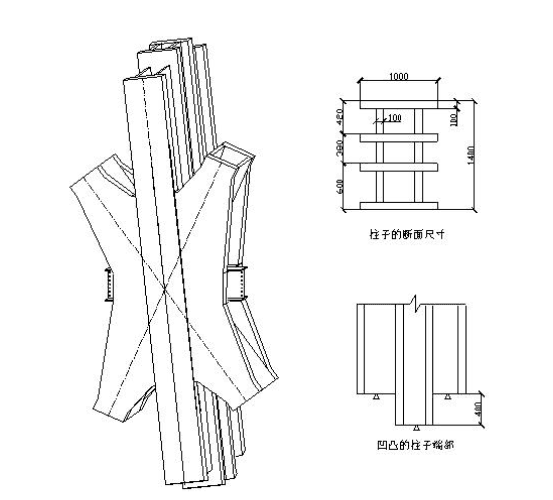
3 问题提出
①厚板焊接的收缩量的大小和制作时的预设。
②焊接变形预防和纠正。
③焊接引起的内应力如何控制在最小。
④多箱柱子端部凹凸面的铣加工
⑤多箱柱子的断面尺寸控制
⑥多箱柱的焊接顺序设定。
4 解决问题的思路
①从结构的整体考虑,应将构件拆分为几个独立而自身能稳定的部件,目的是使部件自身焊接内应力保持平衡,而拆分后的部件之间又以自由端相互焊接,这样就减少焊接时部件相互的牵制。同时将部件之间在连接处的材料预放一定的余量来消除部件焊接变形引起的尺寸误差,从而控制了构件整体的变形和将内应力降为最低。将不定的因数转为可预见和可控制的因数。
②在部件的选择上,尽量考虑部件焊缝的对称性,对非对称的焊缝应通过计算及以往工程的经验比较后得出焊接引起的变形量,在零件准备和焊接顺序上下工夫。这也就要求制作和焊接工艺要相结合出对策。
③对此类结构在编制工艺时要一切从焊接的可操作性可控制性出发,安排组装次序。因为一旦构件变形,矫正工作受温度和结构形式的影响而很难进行和奏效,尤其对于多箱柱更为重要。
④正确地应用好钢结构规范上的公差规定的范围,在规定公差的基础上考虑余量的设放,从而保证产品在合格的范围内。
⑤要建立一套较完整的工艺编制和审核制度,其好处是在工程的开工之初就能预计到工程进行中的问题,即自己提问题和解决问题,把构件的制作在文件上先画圆了。
⑥根据构件的节点形式,多箱柱的验收标准的设定以满足安装需要、满足规范为原则。
5 外框角柱制作工艺
5.1部件的拆分
①根据埋入式柱的结构特点将构件拆分为地上段、埋入段、底板、可拆分的斜撑箱形牛腿、不可拆分的斜撑箱形牛腿等五个分部。
②在拆分段的连接处预放用于铣削、调整位置用的二次切割余量。
③规定了这些部件制作成形后的测量基准。
5.2 构件的制作方法
5.2.1构件的制作流程安排
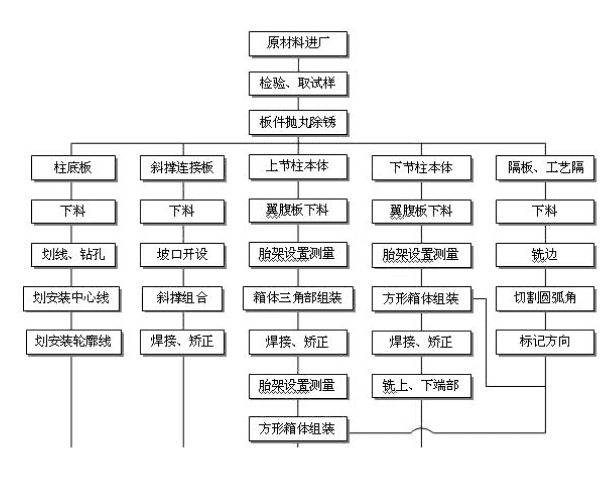
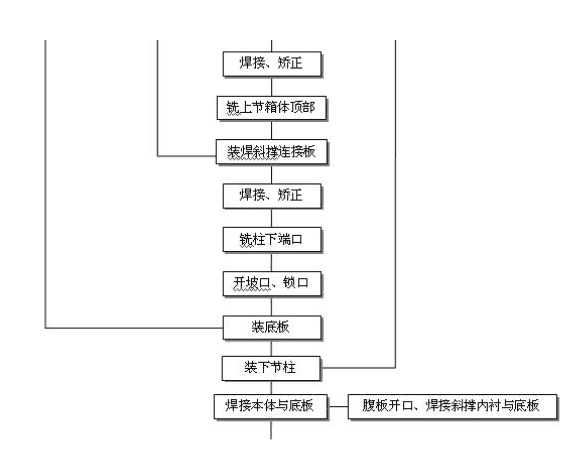
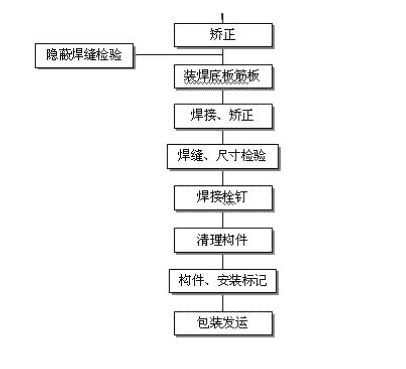
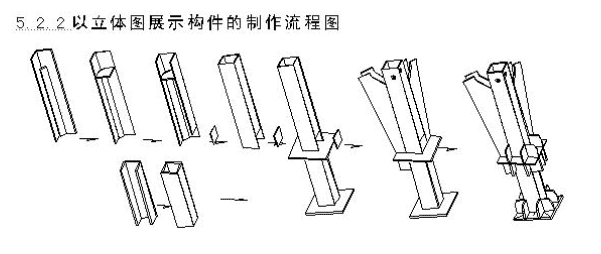
5.2.3上节菱形角柱的制作步序
第一步:①由于菱形箱体内有80mm的斜撑连接板的支持板,此板与菱形箱体的 腹板为焊透焊缝。如菱形箱体组成后再焊接此板,目前条件行不通。因此先以下图三角组件开始。
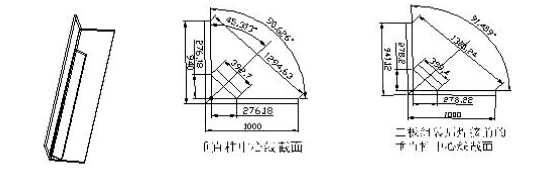
由上图可以看出,三角组件在组装时要考虑三条纵缝在焊接时的焊 横向收缩量和收缩引起的截面变形的协调,根据焊接工艺试验的数据,同时考虑实际焊缝为拘束状态的角接焊缝,因此横向收缩量的大小取2~3mm。而在这里的根据此数值调整三角组件的装配角度从90.626调整为91.459度,同时由焊透焊缝引起的角变形根据经验设置为1度,此角度是在纵缝打底焊完成后用火工完成。焊接接后使截面回复到图纸尺寸。
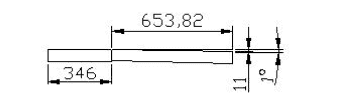
②三角段在纵缝焊接时还存在扭曲问题,因此在三角组件的内部结构上采用工艺隔板,目的是增加面板在焊接时的抗扭刚度,缩短扭曲的计算长度。同时在焊接时采用同规范、同方向的焊接顺序。
③为了减少三角组件在长度方向的拱曲,两翼板间的焊缝仅焊1/2高度,目的是在组合成方箱体时,使方箱体的四条纵缝在焊接时对称进行,减少箱体在长度方向的拱曲变形。
第二步:
①由于构件在垂直于轴线的截面为菱形,必须采用工艺隔板来保证截面组装后的形状。因此在胎架上固定三角部分的一块翼板,加隔板和工艺隔板,利用隔板调整另一腹板扭曲。加另外两块翼腹板,组合成方箱体。
②焊接箱体四条纵缝时,构件必须多点垫实。以防焊接时焊缝收缩和构件自重引起的弯曲和扭曲变形。
③焊接完成的部件必须要进行过程中的变形检验,要有检验人员的参与,因为对此类刚度特大的构件,部件的合格决定了构件的合格。
④焊接后的箱体其焊缝及焊缝附近1倍板厚的位置其应力已达材料的屈服应力,因此后焊的零件对箱体的变形影响不大。此时可对箱体进行铣削定长。铣削后的上段柱放3mm的与底板焊接的焊接收缩余量。
第三步:下节柱的制作过程略同上节柱,工艺隔板选用2块,柱本体焊接完成后,铣本体端口。定长时长度放6mm的与底板焊接收缩余量。
第四步:大斜撑连接牛腿的制作
a.大斜撑牛腿有2种形式:
①可单独制作的斜撑牛腿(图1);
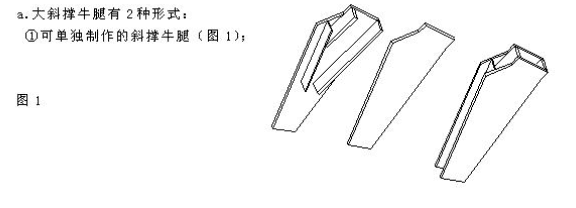
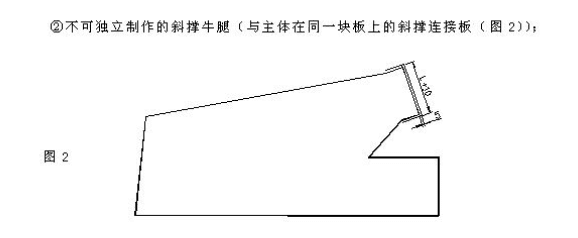
b.制作过程
①图1中可单独制作的斜撑牛腿的制作要点是斜撑连接板要按图纸的最大轮廓切割,单独组合焊接完成后的斜撑牛腿与柱本体的焊接边要进行二次切割,以适合变形后的本体,目的是保证焊缝的尺寸间隙和保证斜撑上口与柱上端口的相对尺寸。
②图2与主体在同一块板上的斜撑连接板在下料时其上端与斜撑连接口的3条边均应放宽5mm的调整余量,原因是此板是上节柱箱体的翼板之一,本体的纵缝焊接收缩导致斜撑上端的位置移动。本体焊接完成后可切除余量。在此板上组合牛腿的其余部分,当焊接另一斜撑连接板时要考虑焊缝收缩时导致的整个牛腿转动,解决的方法是在保证焊缝间隙时调整斜撑连接板的宽度。
第五步:底板
①柱底板由数控切割外形。底板上的锚栓孔由钻小孔后火焰切割而成,检测 切割面,打磨或补焊(按焊接作工艺要求)孔表面。在底板的上、下面画出柱本体的轮廓线,用于组装。
第六步:总装,要求是使上、下节段的柱的中心线调整在一条直线上。
①胎架为水平状态。调整胎架间的高差小于3mm。放入上、下段后,复查上、下柱段的对齐状态。
②在柱底板的向上面必须画出柱的安装轮廓,十字中心线的位置。
③将135mm厚的有孔底板插入柱间,与上节柱点焊在一起。
④推动下节柱顶紧底板,点焊焊接处。
⑤测量安装位置的是否准确,焊接收缩余量是否设置。在胎架上焊接底板与柱身直到完成。
⑥矫正底板,焊接栓钉,清理构件表面,完成各类标记。
6 外框三箱柱
6.1部件的拆分
①根据多箱柱柱的结构特点将构件拆分2个л和1个箱体、2个蝶形节点和牛腿等七个部件。
②在拆分时考虑各部件的焊接收缩余量和铣削余量。
③规定了这些部件制作成形后的测量基准。
6.2 三箱柱子的制作方法
6.2.1 构件的制作流程安排
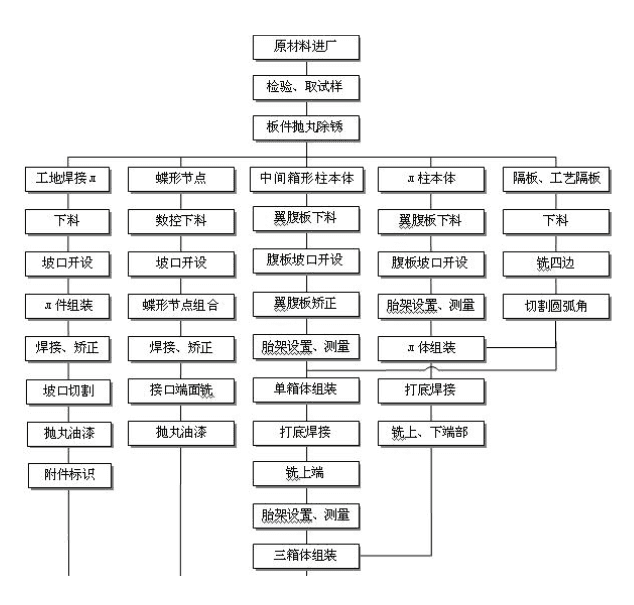
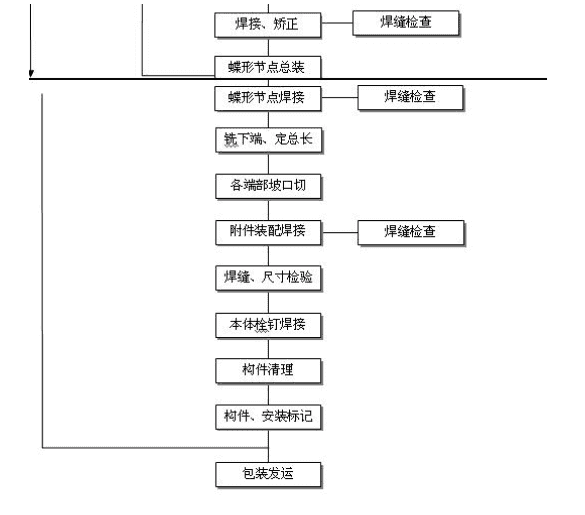
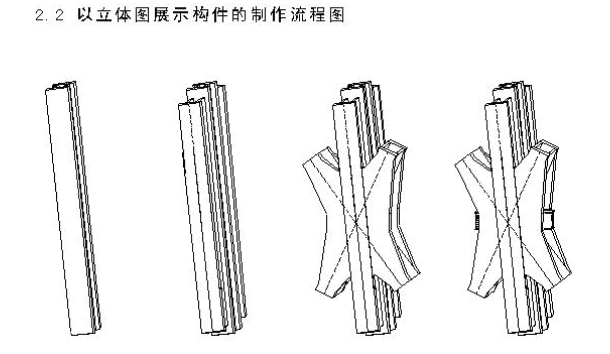
6.2.3三箱柱的制作步序
第一步:三箱柱本体
①由于三箱柱的现场焊接需要,柱子端面设计为凸台形,整体焊接后无法铣削,所以把三箱拆散分别组装,中间为典型的箱形柱,二边为л形柱,由于三箱柱焊接后的刚性很大,而且内侧翼板成形后无法进行矫正,矫正的量及其有限,所以从一开始就要进行变形控制,如:翼腹的旁弯、拱度矫正,使其直线度控制在3~4mm以内,而且弯曲的方向最好一致,避免部件组装后扭曲。装配的胎架进行校平,保证装配的质量。测量工艺隔板和隔板的对角线,使其在装配时处于同向。
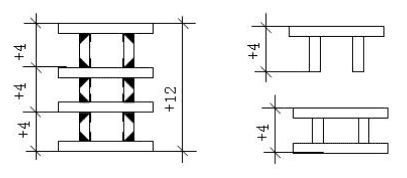
②从上图可以看出,三箱柱在断面高度方向中有6条全焊透焊缝,根据试验数据和加工经验每条焊缝放2mm收缩余量,每个部件放4mm收缩余量,则在三箱柱的高度方向总共放焊接收缩余量12mm。
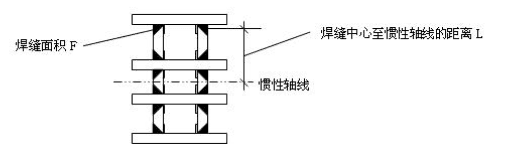
③为了减少焊接变形(拱度方向),在焊缝设计时尽量保证焊接收缩的对称性,见上图,按下列公式进行校核:
Σ上F×L =Σ下F×L 。如果差异很大,应调整焊缝坡口的角度和间隙(焊缝面积)来解决。
④为了端面的铣削需要,先分别对箱形柱和л柱进行打底焊接。
第二步:
①箱形柱只铣上端面,л柱按图纸尺寸上下两端均铣削。
②为了增加本体刚度减少焊接变形,部件不进行埋弧焊,必须待三箱柱组装后进行焊接,三箱柱组装时上端按图纸尺寸进行拼装,也就是说只保证上端凸台尺寸,然后进行三箱柱的纵缝打底。
③为了防止焊接变形,在埋弧焊焊接时应尽量按轴心线进行对称、同步、同向、同规范焊接,同时为了控制拱度,在焊接过程中应进行翻身焊接,不能一次焊完。外侧翼板在焊到1/2焊高时,应及时进行矫正。焊接顺序见下图,先焊距离中心较近的焊缝,再焊距离中心较远的焊缝。本体焊接完成后必须要进行过程中的变形检验,特别是外测翼板,要有检验人员的参与,因为对此类刚度特大的构件,如果把部件的变形放到构件成后再矫正就很困难。
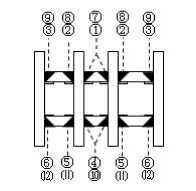
④本体矫正后进行焊缝的UT检查,有缺陷及时返修,最后按图纸的长度尺寸进行柱子下端的总长铣削,以柱子两端口的中心划出修正后的中心线,确定蝶形节点的中心基准线,同时测量下端凸台的尺寸,调整现场焊接的π段长度。
第三步:蝶形节点
①首先在蝶形板上划出基准中心线,按基准线组装蝶形节点,腹板的高度同样放4mm焊接收缩余量,在斜撑连接口处放3mm铣削余量,焊接后矫正蝶形板的平面度。
②划出端口基准线,铣削上下连接端口。以柱子本体中心基准线到翼板边缘的实际尺寸,切割蝶形节点与本体的焊接坡口,安装衬垫板时放出2mm的焊接收缩余量。
第四步:总装
①装配蝶形节点,要求蝶形节点的各个连接端口与柱子本体在同一个平面内,在组装前先调整胎架的水平,测量蝶形节点各端口与本体的平面度(使其控制在5mm范围以内),测量各端口的坐标尺寸。
②蝶形节点焊接时,应以柱子为中心进行对称焊接和翻身焊接,不能一次焊完,减少焊接变形。
第五步:
①装配牛腿和其他吊装附件板,焊接、矫正附件板。对柱子进行整体的测量和检查。
②焊接栓钉,清理构件表面,完成各类标记。
7 总结
通过合理的部件拆分,控制部件的焊接变形来达到构件整体的合格。采取有效的制作工艺措施和焊接控制措施,严格的工艺控制和检验,确保了箱形柱的制作质量,从而加快了制作进度,并经多方检验和最终安装检验,符合设计要求。现场安装一步到位。
参考文献
1.《焊接设计》 (美) O.W.勃劳杰
2.《钢结构设计规范》 GBJ50017-2003
3.《钢结构工程施工质量验收规范》GB 50205-2001